SPIRAL-WOUND GASKET (SWG)
Spec. TU 3689 - 010 - 93978201 - 2008
Spiral-wound gasket was developed at the beginning of 20th century to meet the growing demands of the petroleum refineries. At present this is the most common type of flange gaskets. The spiral-wound gasket became popular owing to a great variety of available designs and sizes.
Spiral-wound gaskets may be made of any weldable metal which is available in the form of a thin strip, so they can be used practically in any aggressive environment in the whole range of temperatures from cryogenic temperature to 1000°C and pressures from vacuum to 42MPa (refer to the article to learn about the list of operating environments where graphite seals can be used,). Spiral-wound gaskets are made by winding alternate layers of carcass (V-shaped metal tape) and filling material (tapes TRG, PTFE or mica) to a former.
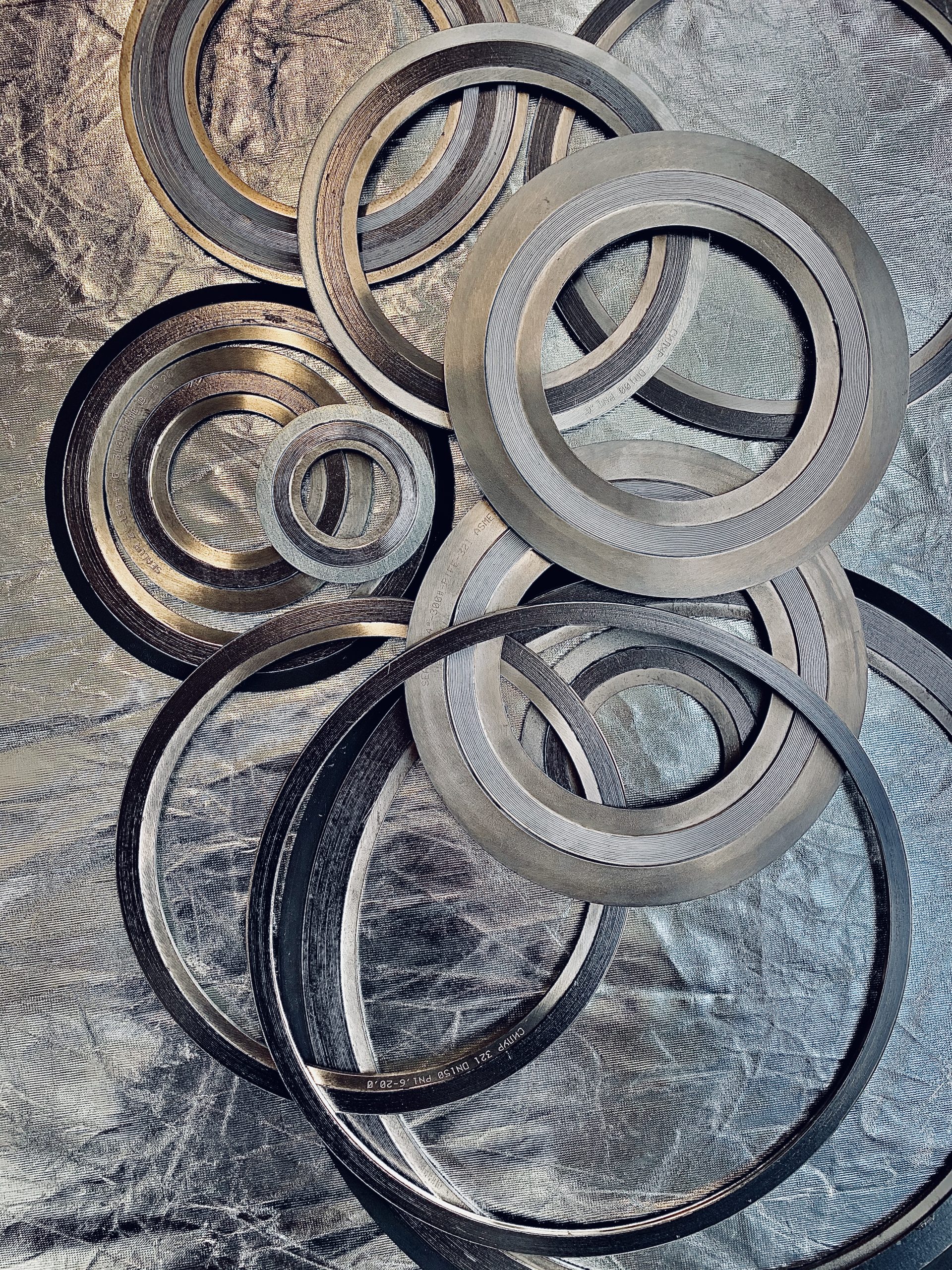
Properties
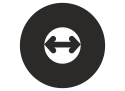
10 ÷ 1600 mm
Conditional pass (DN)
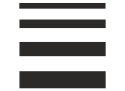
2,3 ÷ 6,5 mm
Shim thickness (inclusive)
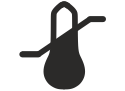
-253 ÷ +1000°С
Acceptable temperature range
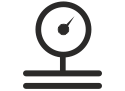
≤ 42 MPa
Permissible pressure the environment
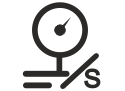
69 MPa
Specific compression pressure
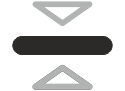
30%
Compressibility
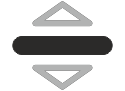
15%
Recoverability
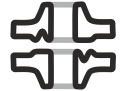
5% (<0,2 mm)
Compensation of the depth of defects in the sealing surface of the flanges relative to the thickness of the gasket,%, but up to _ mm
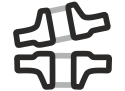
7% (<0,45 mm)
Compensation of non-flatness of the flange connection relative to the thickness of the gasket,%, but up to _ mm;

1,7% (<0,06 mm)
Opening of the flanges, which maintains tightness (P=2.5 MPa) relative to the thickness of the gasket,%, but up to _ mm;
Purpose
The gaskets are made to the sizes in compliance with standards
GOST R 52376, GOST 28759.9 (draft), OST 26.260.454, ASME B16.20, EN 1514-2, EN 12560-2
and are intended for sealing in flanges in compliance with standards
GOST 33259, GOST 28759.3, ASME B16.5, ASME B16.47, EN 1092-1, EN 1759-1